How to shrink wrap a 50-foot boat
Steve Lima turns on what looks like a diesel hairdryer. Although the blue flame it produces is only visible by its base, the heat coming off of it suggests something more massive.
“It’s basically a propane, open-flame gun,” said Lima, the service manager at Concordia Company. The hose running out of the handle hooks to a gas tank on a tool cart, where another gun sits… but this one has a seven-foot extension.
The tools are a necessity this time of year, when Concordia staff are winterizing the boats. This includes running antifreeze through pipes to protect the plumbing systems and engines, but also shrink wrapping the boats to shield them from the elements.
“You wand that over the plastic,” said Lima, moving the gun in a smooth back-and-forth pattern. “The plastic heats up and starts to shrink.”
But covering approximately 100 boats — ranging in size from 50-feet to smaller powerboats — is no easy task. The “hauling season,” when boats get pulled out of the water to be winterized, begins in early September, and will last until mid-December.
“That’s the trick part during this time of year,” said Lima. “The typical weather pattern for the fall… you don’t get three to four non-windy days to shrink wrap.”
Employee Joe Almeida has been working at Concordia for nearly seven years. He takes charge of shrink wrapping boats.
“Joe has a good system,” said Lima, describing the tricks and cheats that Almeida has handcrafted as good, old Portuguese ingenuity.
Almeida starts by creating a backbone for the boats out of wooden dowels. He connects the posts with nylon rope, and secures them along the center of the boat, creating a high point that will suspend the plastic above the deck. When spring comes again, Almeida will bundle the backbones used on each boat and label them so that he can reuse them next winter, saving him the time of having to make ridgelines all over again.
Then, he creates a bellyband — nylon rope tied around the widest part of the hull. The plastic will tuck into the bellyband so that it doesn’t fly off.
Next, Almeida has to unfurl 200-pound rolls of plastic and drape the sheets over the tops of the boats. For this, Almeida has devised a contraption to help.
Most people pull out and measure the plastic inside, bunch it all up, carry it out and up onto the boat, and then try to drape it down the sides, Almeida explained. However, he has rigged a forklift with a hanger for the roll of plastic wrap. This way, he is able to drive the heavy rolls out to the boats, and lift them to the height of the deck, where he can easily unroll one across the boat.
“I went to Ace, and I got all the piping,” said Almeida. “I did that during lunchtime.”
Almeida even considered how the plastic is folded. He explained that by positioning the roll upside-down, the plastic wrap unfolds itself as he unrolls it, saving him another step. Almeida designed and built the piping for two forklifts… one gets 10-feet higher.
The plastic rolls come in various widths — the most common being 26-feet wide — but all weigh approximately 200 pounds, said Almeida. He punched some numbers and created cheat sheets that tell him how many pounds of plastic he needs for various boat lengths, saving him the trouble of measuring it out.
Once Almeida has draped the plastic over the boat and tucked it into the bellyband, he starts heating it up with the torch.
“You get the bellyband first so it’s held tight. Then you start at the bow and work your way back,” said Lima. A seven-foot torch extension helps the men reach over boats from a ladder.
Usually, Almeida heats the plastic one panel at a time until he’s worked his way around the boat, and that requires him to consistently move the ladder, but this year, he’s added a new contraption to help him go faster.
He added bracing to the ladders so that he can secure planks between two of them, much like scaffolding. This way he can walk back and forth easily without having to go up-and-down a ladder.
“This is 10 times quicker now,” he said. All-in-all, each boat still takes up to four hours to shrink wrap, but there are some quirks to watch out for.
“You can shrink wrap over a gel coat, but not over paint,” said Lima. “The moisture gets caught under the shrink wrap, and [the paint] bubbles.”
Because the guns generate so much heat, the team also has to be careful it doesn’t melt holes through the plastic.
“You have to let it cool because it generates heat underneath [the plastic],” explained Lima.
As the wrap heats up, it shrinks to fit the boat. Almeida explained how this works. When the plastic is made, he said, it’s heated up so that it expands. However, the plastic is then secured at its increased size so that, as it cools, it remains enlarged. Then it is folded and transported in rolls.
After Almeida heats up the wrap, it will cool and again shrink to its original size, he said.
The plastic can’t be reused next year like the wooden dowels, but it is recyclable, said Lima.
The most challenging part of the endeavor, despite Almeida’s ingenuity, is the cold. Ice can build up on the boats, making ladders and decking slippery, and the process dangerous, said Lima. The cold weather doesn’t bother Almeida though.
“The people who get cold are the ones not working,” he laughed.
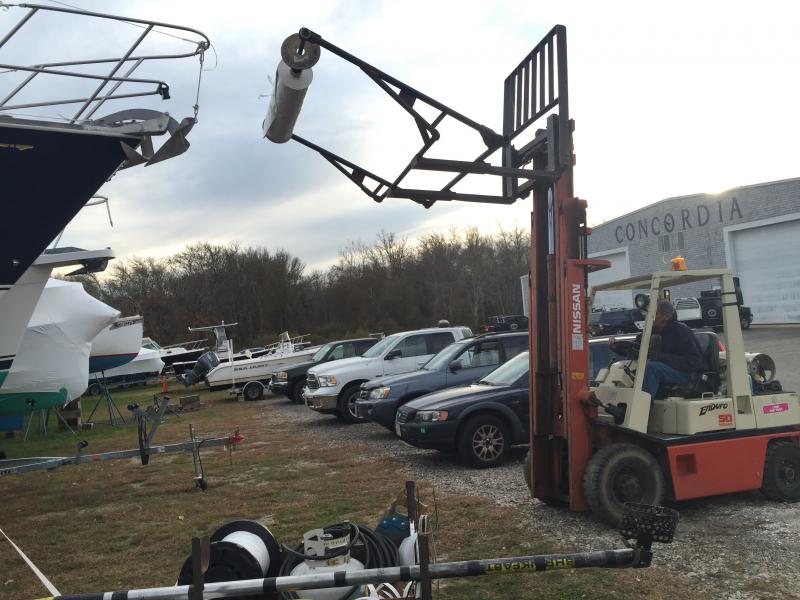
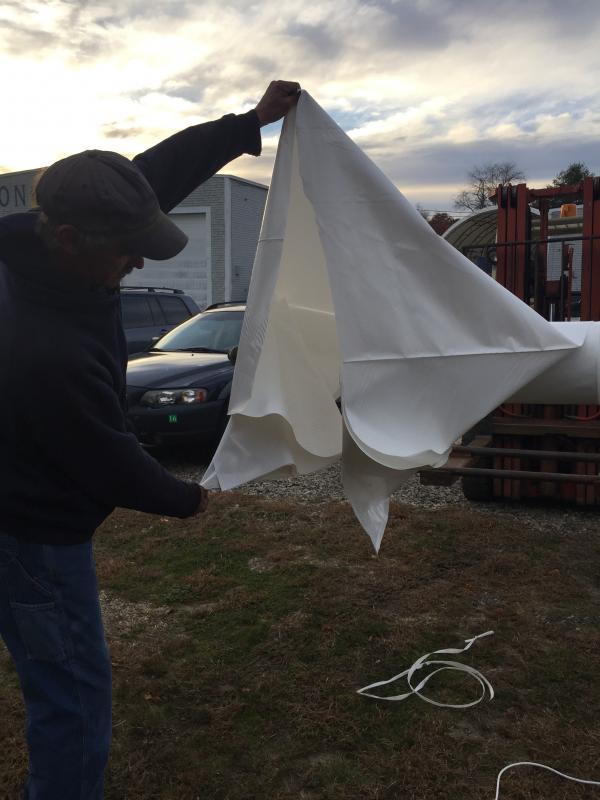
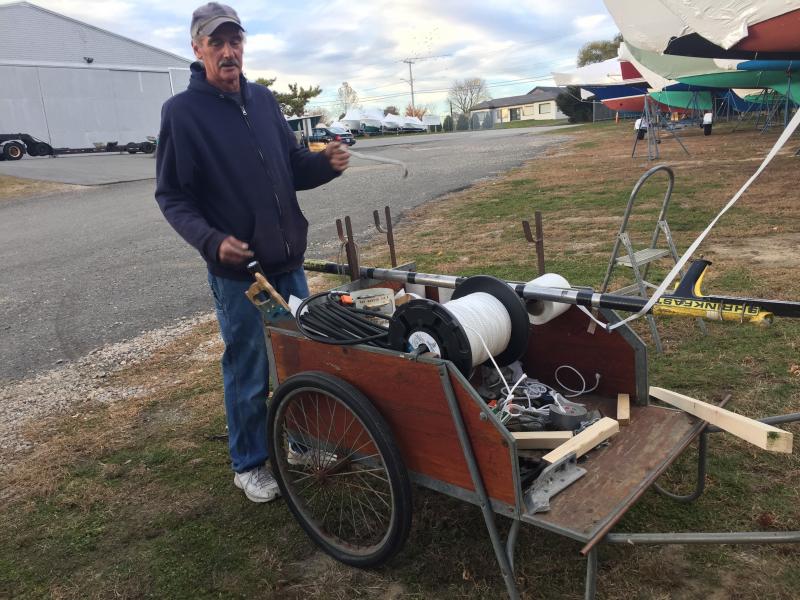
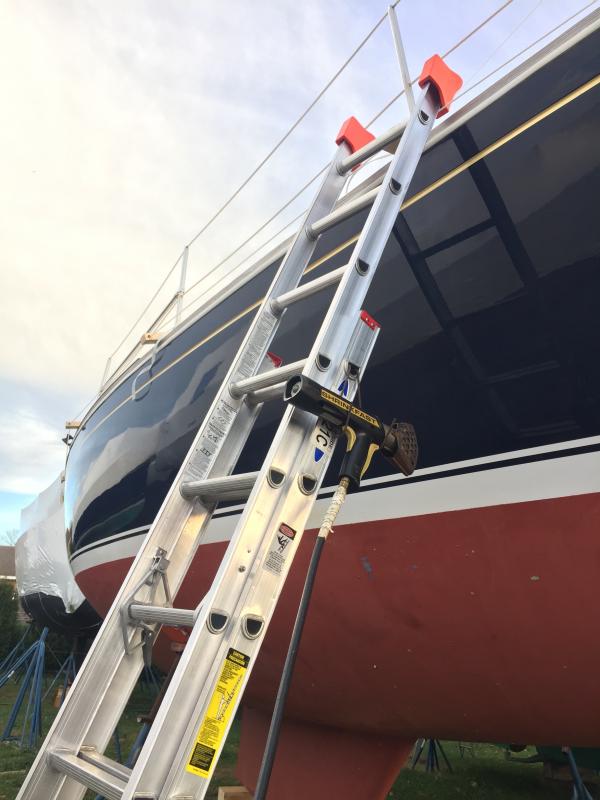